France: Process Heat Application at Viessmann’s Faulquemont Factory
February 17, 2011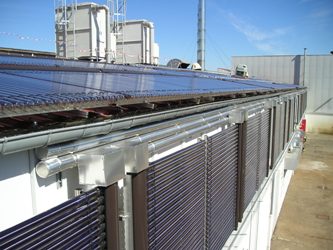
German heating systems manufacturer Viessmann operates a solar process heat system at its factory in Faulquemont, France. 260 m2 of the new heat pipe vacuum tube collector Vitosol 200-T have been installed on the roof and at the facade of the building. The system is used for heating up an alkaline cleaning bath to up to 60°C, in order to degrease hot water storage units before enamelling.
Photo: Viessmann
The Vitosol 200-T vacuum tube collector line was launched at the beginning of 2010. The tubes are produced in Viessmann´s factory in Dachang near Beijing and assembled in Faulquemont. What is so special about them? Vitosol 200-T is the first single glass heat pipe that can be mounted horizontally. So far, heat pipes always had to be installed at a certain minimum angle to ensure the heat is transported properly within the tube. After all, the hot and vaporised heat-transfer medium has to reach the heat pipe condenser and finally flow back into the heat pipe to be heated up again.
In order to allow horizontal installation, Viessmann’s developers have used two tricks. First, the condenser has almost the same diameter as the heat pipe itself. That is to make sure that heat transfer fluid cannot be held back in the well of the condenser. Second, the volume of heat transfer fluid and its viscosity are important to guarantee the condensation of the fluid and transfer it back into the tube.
Solar-heated alkaline bath for degreasing hot water storage units as preparation before the enamelling process.
Photo: Viessmann
“We are more than satisfied with the performance of the Vitosol 200-T system,” Marc Vigneron, General Manager of Viessmann Faulquemont, confirms. “Especially during the summer months, the highly efficient solar collectors provide the necessary heat for the alkaline cleaning bath. All in all, it saves us an equivalent of 10,000 litres of oil every year”, says Vigneron.
In Faulquemont, Viessmann produces solar collectors and hot water storage units designed for a high vertical integration. As far as storage units are concerned, all production steps from the pressing of the cover and the base to the different welding steps and the enamelling are completed on site. Even straight-tube heat exchangers can be produced from scratch with initially in-house developed machines. “We process around 2,500 km of heat exchangers from 3,500 tons of steel annually,” says Vigneron.
The production of the collectors, from cutting the frame components to coating the absorber plate, and assembling the panels is also completed in Faulquemont. The latest investment in the collector division went into a laser welding machine from Austrian supplier Dtec. With two welding chambers and two laser sources each, the machine reaches a cycle time of 70 sec per absorber. Now, the next challenge is to match this frequency with the bending machine.
More information:
http://www.viessmann.fr