Germany: Polymer Collector Design for EUR 25 Production
March 31, 2015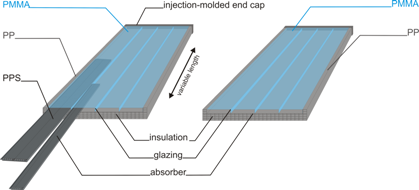

Figure: ISE Freiburg
The collector design joins an extruded absorber profile to injection-moulded end caps, combining the best results from former research projects. The key elements are the several layers of extruded multi-wall sheets. Water will run through the chamber in the upper layer or a separate absorber (see drawings), whereas the chambers in the lower layers will be filled with air and are going to function as insulation for the collector´s back side. Larger chambers will allow air convection and therefore increase thermal losses.
Stagnation temperature control sets efficiency limits
“The idea is to adjust the chambers based on climate conditions, so that the collector will be set to a specific stagnation temperature by controlling temperature losses,” Andreas Piekarczyk from Fraunhofer ISE says. What is particularly important for polymer collectors made of PP is protection against overheating, as the material is only stable up to around 100 °C. Because the stagnation control method used for the PP collectors is going to increase thermal losses, collector efficiency will be 20 % lower than for conventional flat plate models. The collectors are intended for use in non-pressurised drainback systems in which water serves as the heat transfer fluid.
PPS, the second material which was examined, can support up to 250 °C. Hence, it requires little stagnation control, leading to an expected efficiency which is similar to metal-based collectors, so the conclusion by the ISE research group. Because of the extrusion process, it is easy to scale collector length to customer requirements, although it has very little impact on prices per m². At a production rate of 350,000 collectors per year, the extrusion process is very inexpensive. Actual production costs for the absorber unit are below EUR 5 for a PPS collector and below EUR 4 for a PP collector with 1.15 m² of absorber area. Material costs stay below EUR 15 for PP and are little more than EUR 27 for PPS (see the chart below for data per m²). In addition, the PPS collector’s greater temperature resistance will require a selective coating, which will add EUR 5 to production costs.
Polymer collectors should have market price below 100 EUR/m²
With regard to the economic evaluation of the design, the Fraunhofer ISE scientists gathered market prices of collectors of data sheets, through web research and directly from manufacturers. They wound up with an average market price of 230 EUR/m² for flat plate collectors, with the cheapest models costing around 100 EUR/m². Assuming that production accounts for 24 % of the market price (according to common cost structures), average production costs would amount to 55 EUR/m².
The market price for conventional flat plate collectors means that polymer collectors should have a market price below 100 EUR/m². Based on the same cost distribution and the calculated production costs for polymer collectors, PP collectors could price at an acceptable 92 EUR/m². PPS collectors resulted in EUR 170/m² – seemingly too high for low-cost thermosiphon systems.
Collector model |
Average market price of flat plate collectors |
PP collector, estimated at 20 % lower efficiency than flat plate, withstanding up to 100 °C |
Price difference to flat plate collectors |
PP collector with PPS absorber, estimated at similar efficiency as flat plate collector, withstanding up to 250 °C |
Price difference to flat plate collectors |
Production costs per m² collector area |
55 EUR/m² |
24 EUR/m² |
-56 % |
45 EUR/m² |
-18 % |
Net market prices per m² collector area |
230 EUR/m² |
92 EUR/m² |
-60 % |
170 EUR/m² |
-26 % |
Comparing averaged costs and prices of flat plate and polymer collectors. The flat plate collector figures result from market research and from calculations based on common cost structures; the polymer collector figures were based on calculations made during the ExKoll project.
Source: Fraunhofer ISE
Limited impact on system prices
Despite a great reduction in material costs, there is little effect on consumer prices for the entire solar system, as market studies by Fraunhofer ISE show. Taking into account the reduced efficiency and the fact that most other costs, such as for the installation and distribution, stay roughly the same, the researchers consider a realistic estimate to show a total cost reduction of 8 to 16 % per system compared to conventional flat plate collectors. When looking at system prices, the polymer collectors would be most suitable for thermosiphon systems, because collector costs are more relevant to manufacturers of thermosiphon installations than to ones of pumped systems.
Sunlumo also works on polymer thermosiphon system
The One World Solar Collector by Austrian company Sunlumo, however, is based on a different design. The company’s pilot production line in Upper Austria has produced several hundred assembly groups and collectors in the summer of 2014. They are now being field-tested.
Sunlumo has not published any information about the materials used in the manufacturing of the collectors, nor has the company provided any specifics on the production process – besides the fact that conventional plastic processing methods, such as injection moulding and extrusion, are being employed to manufacture components and process semi-finished products. Sunlumo stated that production costs were 50 % below conventional flat plate collectors, but no absolute figure was given. Pipe systems, pump groups and storage tanks made of plastic are in the works.
Sunlumo´s idea is to license the technology to partners in different countries. The company does not publish information about already sold licenses. According to its Managing Director, Robert Buchinger, the pilot production line is to showcase production to interested investors and manufacturers. Sunlumo intends to offer pumped solar water heating sets with 4 to 6 m² of collector area for below EUR 1,000 (excl. VAT) to end customers in central Europe.
More information:
Sunlumo: http://www.sunlumo.at
IEA SHC Task 39: task39.iea-shc.org